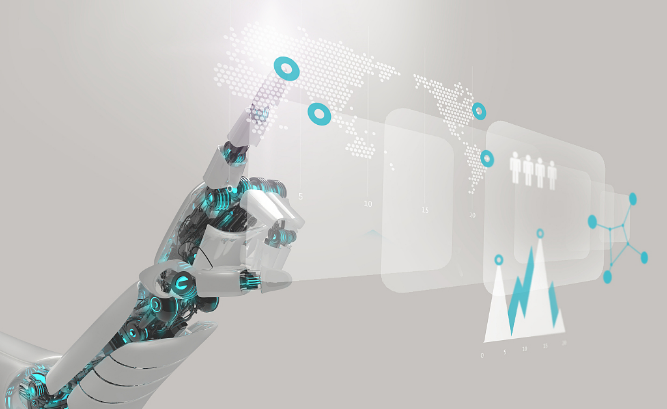
如何 找到合适的激光切割机
对于大多数制造商来说,购买工业激光切割机是一个重大决定。光纤激光器是激光切割机的激光源,它将聚焦于工作区域并切割材料。它与您投入的初始资本以及对整个制造过程的影响息息相关。如果选择了错误的机器,您将不得不在相当长的时间内承受这一决定。这种类型的设备支出数额巨大,因此制造商应该知道如何找到合适的设备。
你知道如何挑选一款适合自己的吗?即使你现在有一款,你是什么时候买的,它对你有什么影响?
本指南将帮助您做出正确的购买决策,将您的制造业务推向新的高度。
如果您的公司将工作分包给其他工厂,或者您在交货时间方面具有灵活性,那么您实际上不需要投资激光切割机。同时,这种情况不会带来太大的风险。但如果您在激光切割零件上花费很多,您可以考虑在公司内部使用光纤激光切割机。用亨利·福特的话来说,“如果你需要一台机器却不买,那么你最终会发现你付了钱却没有得到它。”
出于多种原因,投资不同的自动化系统对公司来说可能是有意义的。它可以帮助我们降低购买选择的风险,因为我们可以调查和分析哪一个可以满足我们的需求。
如果您决定购买激光切割机,那么问题来了:如何选择合适的激光切割机?您可以考虑以下几点后做出选择。
1.CO2激光器和光纤激光切割机的激光技术有什么区别?
目前,两种类型的激光器占据了工业市场的绝大部分:传统的二氧化碳气体激光器和新型光纤激光器。二氧化碳激光器长期以来一直占据市场主导地位,它使用充气谐振腔来获取电力,并使用镜子来传输光束。但光纤激光器使用光纤激光发生器作为光源来切割材料。早期的光纤技术只能在薄材料上以更高的速度切割,但随着更强大的激光器的出现,光纤激光器即使在 0.5 英寸厚的材料中也表现出强劲的切割速度。因此,尽管价格较高,但光纤激光器往往是一种受欢迎的选择。尽管它在 2008 年首次出现,但越来越多的制造商选择购买光纤激光切割机,因为它效率高、运营成本低。此外,光纤技术可以切割反射性材料,例如铜和黄铜,而二氧化碳激光器则很难做到这一点。但对于一些较厚和特殊的材料,应用可能更适合二氧化碳激光器。此外,一些制造商可能对二氧化碳技术感到满意,因为他们已经使用了好几年,而且公司拥有内部维护专业知识。
2、激光切割机的使用寿命及设备维护:
保修期过后,您还需要考虑另一个因素,即持续维护。您是依赖原始设备制造商的服务还是第三方提供的服务?与 CO2 激光器不同,光纤激光器的可移动部件或镜子较少,因此在其使用寿命期间所需的持续维护较少。光纤激光束通过光缆产生。它们不需要光学镜(昂贵的间接成本),并且其聚焦透镜不暴露。因此,与其他激光器相比,如果维护得当,聚焦透镜可以使用一生。此外,与其他形式的激光器相比,光纤激光器的可移动部件较少,后者利用快速移动的镜子来增加激光的强度。没有镜子,切割速度会提高,维护工作量也会减少。要切割 1 毫米厚的直线,光纤激光器的切割速度是传统激光器的三倍。这包括切割不锈钢等材料。虽然光纤激光切割机的后期使用成本较低,但这并不意味着其运行过程中不需要维护。
由于金属切削加工时会产生大量粉尘,因此必须加强粉尘处理,以保证机床内部部件不受污染,设备有效运行。另外,还必须注意机床的润滑,以及导轨架等齿条的润滑,以提高机床的速度。
3.物料处理。
这也是一个需要考虑的重要因素,因为如今激光切割机的切割速度正在提高,因此了解如何安排生产计划对您来说很重要。您每天计划激光机有多少个工作班次?即使它有第二个交换工作台,您的操作员能否跟上手动装卸激光器的速度?最大限度地降低劳动力成本可以帮助您在业务中保持竞争力。有时钢铁制造商可能选择不立即购买物料搬运自动化。如果您选择这条路线,请确保将来可以轻松添加托盘系统甚至自动存储和检索塔。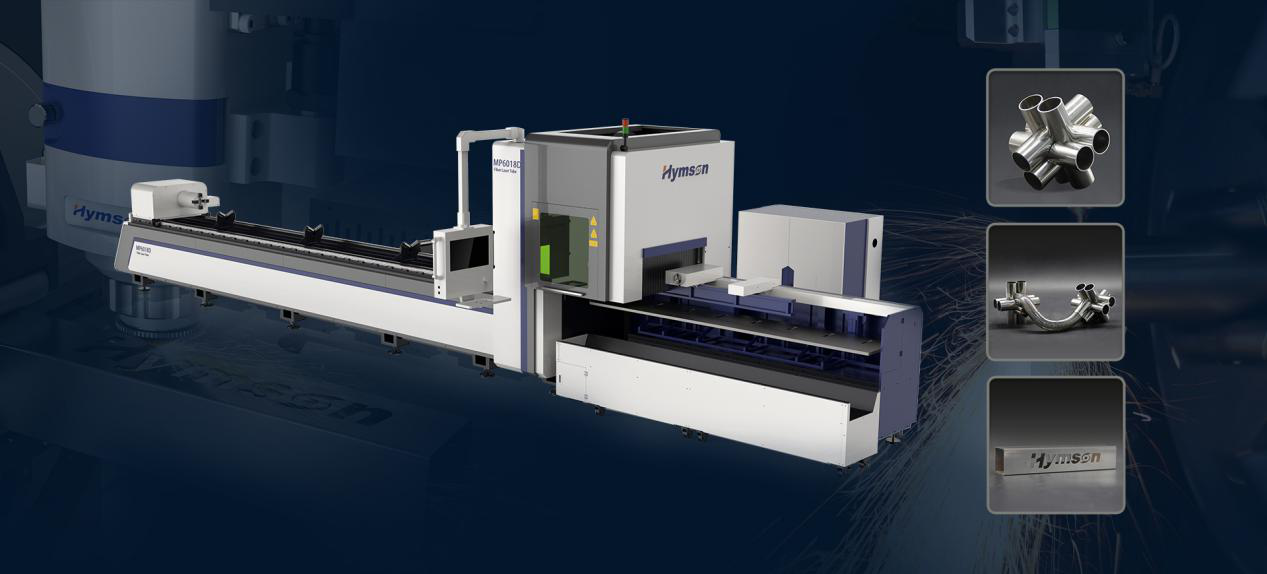
4.光纤激光切割机供应商提供的新软件
● 在许多情况下,制造商都有他们习惯使用的软件包。原有的软件能否在新机器上有效运行,或者您需要购买新软件?新软件能给您带来什么?新软件包能与您的机器配合使用吗?了解不同软件的功能至关重要,这样您才能决定是否需要购买新软件。● 监控软件的成本约为设备价格的 1%,但可以带来 10% 至 50% 的生产力提升,回报期不到四个月。因此,还有一个因素需要考虑,新软件包能否监控整个运营过程并实时衡量其性能?
5、激光切割机的切割激光技术
您需要什么切割技术?根据您的制造情况,选择可以帮助您最大限度提高产量的切割技术。然后咨询您的潜在供应商,并请他们为您提供有关哪种类型的机器可以使您保持竞争力的建议。以下是一些常见的切割技术:● 跨越式切割
新的基于CNC的跳越功能消除了切割头“矩形”运动或假跳越的缺点。
采用抛物线运动,通过跳跃、下降的方式,由CNC实现实时控制,定位准确、快速,大大提高了加工效率,可应用于钣金激光切割。
● 自动避障
当工件翘起时,切割头能自动识别,快速上升避障,并智能定位下一个工件位置
- 减少切割头与工件发生碰撞的概率;
- 保证加工过程中切削的一致性,从而提高加工效率;
- 智能定位下一工件的位置,降低板料整体转移的概率,减少板料的浪费;
- 通过简便、智能的操作减少操作人员和编辑人员的工作量。
● 闪电切割
海目星特色新技术,从切割精度、切割速度、切割能耗三个方面提升激光切割生产效率
高效:闪电切割具有更高效的穿孔能力和更快的切割速度。
低能耗:切割用气体能耗降低50%以上
品质好:切割断面质量较高,切边光滑均匀,毛刺较少。
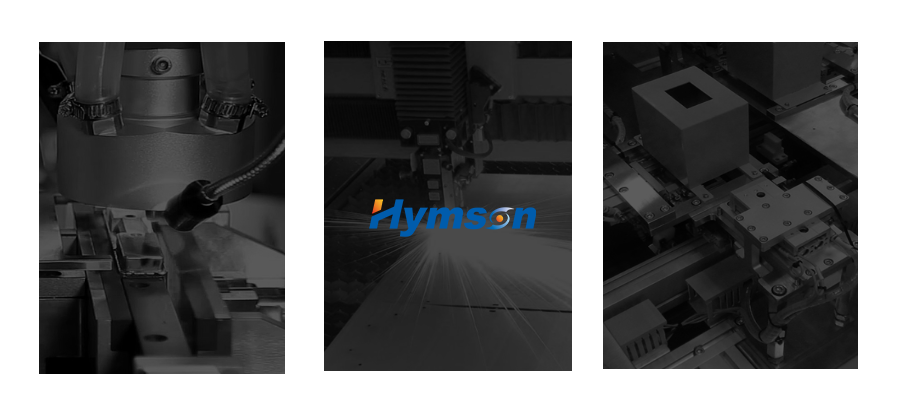
● 快速穿孔
海目星特色新技术,缩短射孔时间,优化射孔全过程,实现稳定、快速、高质量射孔
速度快:200ms内可连续快速穿透各种中等厚度的板材
效率高:比一般打孔时间1-2秒节省80%以上
质量高:穿孔过程稳定,无爆破,安全高效。
操作简便:简洁、智能,减少操作人员和编辑人员的工作量。
● 断点续传
切割过程中如遇到程序中断、突然断电等情况,重新启动机器时,“断点继续”功能可以记忆之前设置的路径并继续加工。
避免从原起点重新进行流程,耗时耗力,影响效率
在切割厚板或者轮廓较宽的工件时,“断点续切”功能可以很好的解决耗时、耗材、成本高等一系列问题。
● 任意点切入
在实际生产过程中,当由于板材上某个节点有灰尘、气体不足等原因造成板材某部分切割不彻底时,一般激光切割机厂家的解决办法是重新设置系统界面,也就是从开始到结束重新走一遍工序操作,耗时、耗材、成本较高。
采用海目星“任意点切入”功能,切割头可以在任意一点切入,无需从头到尾切割,解决了耗时、耗材、成本高等问题。
● 工具启动时逐步调速
厚板切割不彻底,断面线条不均匀,断面挂渣严重等,刀具启动不良会导致厚板无法得到优质的切割效果,出现反光蓝光、断层等一系列影响工件质量的问题,严重时还会损坏切割头及光学器件。
采用海目星“刀具启动渐进调速”(厚板专用)工艺,穿孔后智能渐进调速,切割效果更佳,该工艺主要应用于厚不锈钢、铝合金板材切割,稳定性好,工件质量高。
● 铝合金无毛刺切割(选配)
铝合金切割容易出现毛刺,需要额外进行手工或机械打磨,增加了产品生产工序,从而降低了生产效率、延长了出货周期、增加了生产成本。
海目星“铝合金无毛刺切割”工艺,实现了无毛刺、无皱纹、精度高、无模具消耗、不需修模、节省更换模具时间、节省加工费、降低产品成本等。
● 飞剪
“飞切”工艺可以将轮廓切割的起点放在激光头运动轨迹的切线上,不采用引线,不是单独切割每一个细节,而是将所有轮廓切割成一条直线。
它减少了切割时激光切割方向的变化,减少了穿孔的时间和次数,保证了切割过程中激光头始终处于高速运动状态,非常适合薄钢板的高速切割加工。
减少了板料的加工时间,提高了车床的切削效率。
● 高速切削
一般的急加速、减速,如剧烈的冲击振动、齿条断掉等,都可能损坏车床的硬件。
Hymson的“高速切割”功能预先规划切割路径,并优化车削和加减过程以及插补。
高效:大幅提升加减速性能,减少加减速时间;复杂工件加工效率提升30%
安全:吸收机床切削时加速、减速产生的冲击,保证机床的高速加工,并保护机床免受冲击。
Hymson 激光器可提供以下所有切割技术。有关 Hymson 激光器 -光纤激光切割机供应商的更多信息,请单击此处: cnc 光纤激光切割机制造商 - Hymson (hymsonlaser.net) 。我们可以提供 cnc 金属板切割机、光纤激光管切割机、光纤激光焊接机。
6.我们如何筹措购买资金?
虽然有些制造商会用现金购买激光设备,但大多数制造商会使用其他方式来融资。不要以为银行是购买激光设备的最佳融资来源。考虑其他替代方案,例如 OEM,其中许多 OEM 都有自己的融资部门。考虑以下因素并根据反馈获得报价后,激光切割机供应商的选择可以缩小到两到三个来源。从那里你需要找到合适的型号,在设备演示期间提出正确的问题,并努力达成可接受的价格。请记住,在最终谈判中有很多重要事项需要讨论。
分享这篇文章: