钣金激光切割是一种用途广泛且精确的制造工艺,彻底改变了行业制造复杂金属部件的方式。该技术利用聚焦的高能激光束以惊人的精度和速度切割、蚀刻或穿孔钣金,使其成为广泛应用中不可或缺的工具。
金属板激光切割的核心是使用激光源、切割头和运动控制系统来精确引导激光束沿预定路径进行切割,从而有效地切割金属。与传统的金属切割方法相比,该工艺具有一系列优势,包括提高生产率、改善零件质量和减少材料浪费。
钣金激光切割设备关键部件
钣金激光切割的成功很大程度上取决于其关键部件的集成和性能。这些包括:
激光源
激光源是系统的核心,提供高能光束,使切割过程得以进行。激光技术的进步推动了强大、高效、可靠的激光源的发展,例如光纤激光器和 CO2 激光器,它们常用于金属板激光切割应用。
切割头
切割头负责将激光束精确引导和聚焦到工件上。它通常包括透镜系统、用于输送辅助气体的喷嘴和用于监控切割过程并保持最佳性能的先进传感器。
运动控制系统
运动控制系统是激光切割设备的“大脑”,精确控制激光束或工件的运动,以实现所需的切割图案和几何形状。该系统通常采用先进的计算机数控(CNC)技术,以确保高速、高精度切割。
自动化与集成系统
许多钣金激光切割机都配备了自动化和集成系统,例如材料处理、零件分类和零件标记功能。这些功能可提高生产率、减少人工劳动并提高整体效率。
钣金激光切割的应用
汽车和运输
汽车和运输行业严重依赖金属板激光切割来制造复杂的车身面板、结构部件和复杂零件,充分利用该技术的精度和速度。
航空航天和国防
在航空航天和国防工业中,钣金激光切割用于生产飞机、航天器和军事装备的轻质、高强度部件,这些部件的精度和材料效率至关重要。
建筑和施工
建筑和建筑行业利用金属板激光切割来制造建筑元素、建筑立面和结构部件,利用该技术创造复杂设计和形状的能力。
消费品和电子产品
钣金激光切割也用于消费品和电子设备的生产,能够制造具有卓越质量和一致性的复杂外壳、壳体和精密零件。
选择钣金激光切割设备时要考虑的因素
选择钣金激光切割设备时,必须考虑几个关键因素,以确保最适合您的特定需求:
激光功率和切割能力:设备的激光功率和切割能力将决定可加工的金属板材的厚度和类型,以及切割速度和质量。
切割速度和精度:设备的切割速度和精度对于决定整体生产率和零件质量至关重要,特别是对于复杂或大批量生产而言。
材料兼容性:设备应能够处理各种金属板材料,包括钢、铝、不锈钢和其他合金,以满足制造工艺的多样化要求。
自动化和集成能力:将激光切割设备与其他制造系统(如材料处理、零件分类和零件标记)集成的能力可以显著提高生产力和效率。
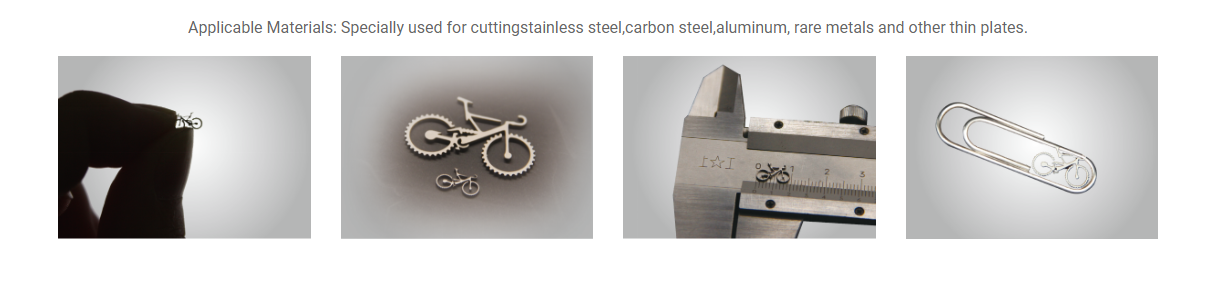
钣金激光切割设备应用
钣金激光切割设备的维护与优化
正确维护和优化钣金激光切割设备对于确保稳定的性能、延长设备使用寿命和实现最佳生产力至关重要。主要考虑因素包括:
预防性维护实践:实施全面的预防性维护计划,包括定期检查、清洁和更换组件,可以帮助最大限度地减少停机时间并确保设备可靠运行。
故障排除和维修:建立有效的故障排除协议,并联系熟练的技术人员进行及时的维修和保养,有助于最大限度地减少生产中断并保持最佳设备性能。
提高效率和生产力:持续监控和优化切割参数,例如激光功率、切割速度和辅助气体设置,可以帮助提高效率、减少材料浪费并提高整体生产力。
结论
通过了解钣金激光切割设备的关键部件、应用和注意事项,制造商可以充分发挥这项变革性技术的潜力,并以精准、高效和创新的方式推动业务向前发展。
分享这篇文章: